Double-Lin Valves
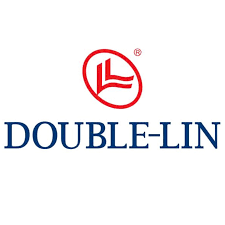
DOUBLE-LIN
Double line valves are essential components in various industrial applications, particularly in the oil and gas sector. Designed to control the flow of fluids, these valves feature two distinct pathways, allowing for precise regulation and isolation of fluid systems. Their dual design enhances safety and efficiency, enabling operators to manage pressures and prevent backflow effectively. Often constructed from robust materials to withstand harsh environments, double line valves are crucial for ensuring reliable performance and minimizing leaks, thereby contributing to the overall integrity of the systems they serve.
https://www.double-lin.com/
1. CHECK VALVES
Double line check valves are typically used in applications where it’s crucial to prevent backflow and ensure the integrity of fluid systems.
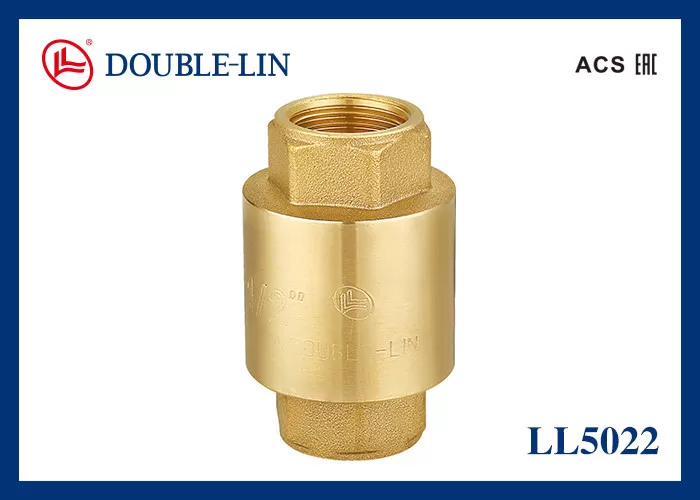
General Specifications
Material:
- Body: Brass, stainless steel, carbon steel, or PVC.
- Seals: Nitrile, EPDM, or Viton, depending on fluid compatibility.
Size:
- Common sizes range from 1/2 inch to 6 inches in diameter.
Pressure Rating:
- Usually rated for working pressures of 150 psi, 300 psi, or higher depending on the application.
Temperature Range:
- Typically operates within a temperature range of -20°F to 250°F, depending on the material.
Connection Type:
- Threaded (NPT, BSP)
- Flanged (ANSI, DIN)
- Socket weld or butt weld options for piping systems.
Flow Direction:
- Designed for bi-directional flow with an internal mechanism to prevent backflow.
Design:
- May include spring-loaded mechanisms for enhanced sealing.
- Some models feature a visual indicator or alarm for monitoring valve status.
Testing Standards:
- Compliance with relevant standards such as ANSI, API, or ISO.
Applications
- Hydraulic systems
- Pneumatic systems
- Water and wastewater management
- Chemical processing
- Oil and gas industries
Additional Features
- Indicator or visual check feature for valve position.
- Optional filters to prevent debris from affecting operation.
- Corrosion-resistant coatings for harsh environments.
2. BALL VALVES
Double line ball valves are commonly used in applications requiring precise flow control in two separate lines, such as in oil and gas, chemical processing, and hydraulic systems

General Specifications
Material:
- Body: Stainless steel, carbon steel, brass, or plastic.
- Ball: Stainless steel or other corrosion-resistant materials.
- Seals: PTFE, Viton, or other suitable elastomers.
Size:
- Available in various sizes, typically ranging from 1/2″ to 6″ or larger.
Pressure Rating:
- Commonly rated for ANSI/ASME classes (e.g., 150, 300, 600 psi).
Temperature Range:
- Typically -20°F to 450°F, depending on the materials used.
End Connections:
- Options include flanged, threaded (NPT), or socket weld.
Functional Specifications
Flow Direction:
- Designed to control flow in two separate lines, allowing for isolation and diverting.
Operation:
- Quarter-turn operation for quick opening and closing.
- Manual or automated actuation options (electric or pneumatic).
Seal Type:
- Soft-seated or metal-seated options for different applications and pressures.
Testing:
- Hydrostatic and pneumatic testing to ensure leak-tight performance.
Maintenance:
- Designed for easy maintenance and replacement of seals and seats.
Applications
- Oil and gas pipelines
- Water and wastewater treatment
- Chemical processing
- HVAC systems
- Power generation
3. PRESSURE REDUCING VALVES
Double line pressure reducing valves are used to regulate and reduce the pressure of fluids in two separate lines, ensuring consistent downstream pressure. They are commonly found in various applications, including water supply, gas distribution, and industrial processes
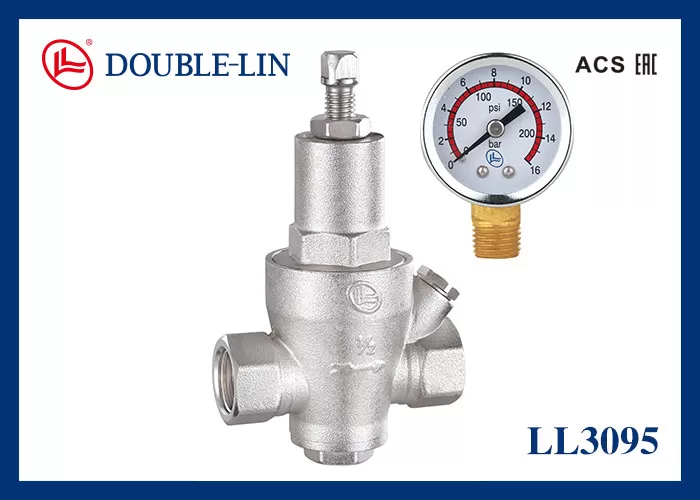
General Specifications
Material:
- Body: Cast iron, stainless steel, brass, or carbon steel.
- Diaphragm/Seal: EPDM, nitrile, or other suitable elastomers.
Size:
- Available in various sizes, typically ranging from 1/2″ to 6″ or larger.
Pressure Rating:
- Commonly rated for ANSI/ASME classes (e.g., 150, 300 psi).
Temperature Range:
- Typically from -20°F to 250°F, but this can vary based on the materials used.
End Connections:
- Options include flanged, threaded, or socket weld.
Functional Specifications
Pressure Reduction:
- Designed to maintain a consistent downstream pressure regardless of fluctuations in upstream pressure.
Operation:
- Spring-loaded diaphragm or piston mechanism for pressure regulation.
- Adjustable setpoint for desired downstream pressure.
Flow Direction:
- Specific inlet and outlet ports to ensure proper flow direction.
Testing:
- Hydrostatic testing to ensure leak-free performance.
Maintenance:
- Accessible design for easy inspection and maintenance, with replaceable parts such as diaphragms and seals.
Applications
- Water supply and distribution systems
- Gas distribution systems
- HVAC systems
- Industrial process control
4. STRAINERS
Double line strainers are essential components used to filter out debris and contaminants from fluids in various applications, helping to protect downstream equipment from damage.
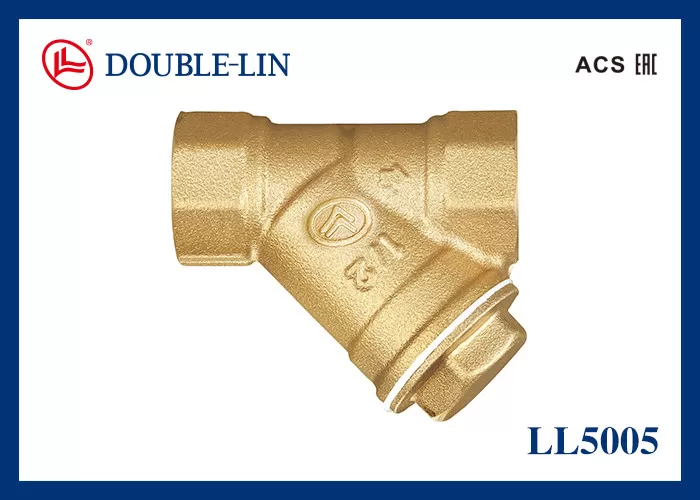
General Specifications
Material:
- Body: Cast iron, stainless steel, carbon steel, or brass.
- Screen: Stainless steel or perforated metal, often with a mesh screen.
Size:
- Available in various sizes, typically ranging from 1/2″ to 6″ or larger, depending on the application.
Pressure Rating:
- Commonly rated for ANSI/ASME classes (e.g., 150, 300 psi).
Temperature Range:
- Generally from -20°F to 250°F, though this can vary based on materials.
End Connections:
- Options include flanged, threaded, or socket weld
Functional Specifications
Filtration:
- Designed to remove particulates and contaminants from fluids, protecting downstream equipment.
Flow Direction:
- Specific inlet and outlet ports to ensure proper fluid flow.
Screen Design:
- Typically available in different mesh sizes and shapes (e.g., perforated, wedge wire) to suit various applications.
Maintenance:
- Easy access for cleaning or replacing the screen, often with a removable cover or blow-off valve.
Applications
- Water treatment and distribution systems
- Oil and gas processing
- HVAC systems
- Chemical processing
- Food and beverage industry
5. GATE VALVES
Double line gate valves are used to control the flow of fluids in two separate pipelines and are particularly valuable in applications requiring tight shutoff and minimal pressure drop.
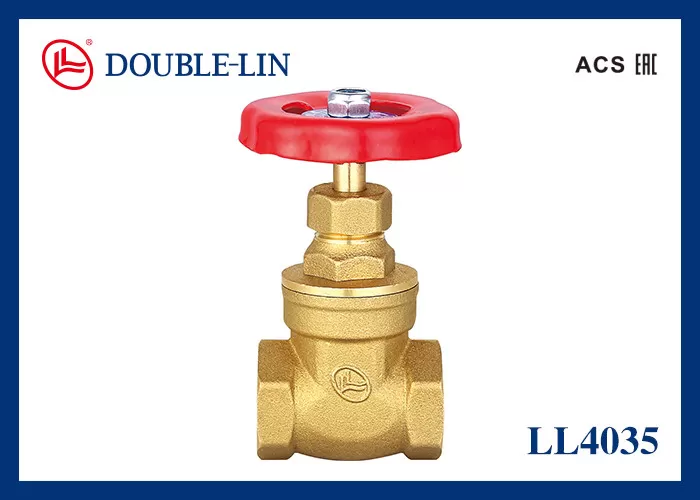
General Specifications
Material:
- Body: Cast iron, stainless steel, carbon steel, or brass.
- Gate: Stainless steel or other corrosion-resistant materials.
- Seals: Elastomers such as PTFE or rubber, depending on the application.
Size:
- Available in various sizes, typically ranging from 2″ to 12″ or larger.
Pressure Rating:
- Commonly rated for ANSI/ASME classes (e.g., 150, 300, 600 psi).
Temperature Range:
- Typically from -20°F to 400°F, depending on materials used.
End Connections:
- Options include flanged, threaded, or butt weld.
Functional Specifications
Flow Control:
- Designed for on/off service, allowing for full flow with minimal pressure drop when fully opened.
Operation:
- Manual operation via handwheel or automated options (electric or pneumatic actuators).
- Typically features a rising or non-rising stem design.
Sealing Mechanism:
- Parallel or wedge-shaped gate design for effective sealing.
- Soft or metal seating options based on application requirements.
Testing:
- Hydrostatic and pneumatic testing to ensure leak-free performance.
Maintenance:
- Easy access for maintenance and inspection, with replaceable seals and parts.
Applications
- Oil and gas pipelines
- Water supply and distribution systems
- HVAC systems
- Chemical processing
- Power generation
6. AIR VENTS
Double line air vents are used to release trapped air in fluid systems, ensuring efficient operation and preventing issues like air locks.

General Specifications
Material:
- Body: Brass, stainless steel, or PVC.
- Seals: EPDM, Viton, or other suitable elastomers.
Size:
- Commonly available in sizes ranging from 1/2″ to 3″ or larger, depending on the application.
Pressure Rating:
- Typically rated for various pressures (e.g., 150 psi or higher), depending on the design.
Temperature Range:
- Generally from -20°F to 250°F, but can vary based on materials used.
End Connections:
- Options include threaded, flanged, or socket weld.
Functional Specifications
Air Release:
- Designed to automatically release air from the system while preventing fluid loss.
Flow Direction:
- Specific inlet and outlet ports to ensure proper function and flow.
Operation:
- Typically uses a float mechanism or a pressure differential to open and close the vent.
Maintenance:
- Easy access for inspection and maintenance, often with a removable cover for cleaning.
Applications
- Water and wastewater treatment systems
- HVAC systems
- Industrial piping systems
- Chemical processing